

Forces and Flexural Modulus
The goal of the project is to determine whether The combination of materials is stiff enough to withstand a force of 40 kips delivered at the center using a 10 in. cylinder. Material properties must be derived from our samples. To achieve this, we performed a three point bending test with specifications of ASTM D2344. The machine used for the test is an MTS TestWorks 4, and a fixture was made for the experiment.
​
Six of the eight samples for each specimen was tested, and its results normalized for a better estimate of the results. The machine delivers a load that causes a deflection of 1 mm per minute the specimen is on the machine until about 15 minutes. A load versus displacement versus strain plot is derived from the results.
​
From this plot, the flexural modulus is derived from the slope of the graph until the material fails. The failure load is also documented as a reference for the finite element analysis. From this plot, the flexural modulus is derived from the slope of the graph until the material fails. The failure load and failure modes are also documented as a reference for the finite element analysis
Equations


Results
The failure for the specimen occurred around 1.41 kN to 5.75 kN, with a deviation of 0.18. BMC, with randomly distributed fibers, had a lowest maximum load but had the most consistent results with the smallest deviation. The other homogeneous material supported lower loads than the sandwiches, with the exception of SMC. Sandwiches combined with the woven composite (Mat) resulted in higher maximum loads. The combination of Mat-SMC, and Mat-BMC also performed about the same, which is evident of Mat good at resisting bending.
The flexural stress of the samples had a trend similar to the maximum load, with the exception of the homogeneous Mat sample. BMC had the lowest value while the Mat sample had the highest. It is noted that the difference is likely due to the difference of the sample thickness between the samples.
​
A stress-strain curve was plotted to derive the flexural modulus of the samples. The results had BMC having the lowest moduli with the Mat trim samples following after. SMC resulted in the highest modulus, but also had the highest deviation amon the rest. This may be due to the defects already present in the samples when tested. No trend was observed bewteen the maximum stress and load, coinciding with the value of the flexural modulus. It is also observed that adding Mat to the structure resulted in an overall increase in flexural modulus.
​
​

The failure modes were recorded in accordance to the ASTM D2344 and ASTM D7264 (Table 5). The consistent modes of failure resulted in interlaminar failure and flexural failure. Interlaminar failure is a crack propagating perpendicular to the direction of the load usually results of the epoxy between two materials breaking before rather than the material itself. Flexural failure occurs when the failure agrees with the beam theory, which occurs when compression at the top of the structure (where the loading nose is located) fails compression, or the opposite side breaks apart in tension.

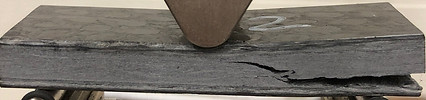
Flexural Failure​
Interlaminar Failure
The failure modes for the homogeneous samples demonstrated a flexural tension failure at the loading nose, except the Mat sample, which showed signs of both interlaminar and flexural failure.
The failure modes for the homogeneous samples demonstrated a flexural tension failure at the loading nose, except the Mat sample, which showed signs of both interlaminar and flexural failure. The Mat-Trim-Mat Sandwiches also had both interlaminar shear and flexural shear both at the supports and the loading. Other sandwiches involving Mat seemed to fail due to interlaminar shear first, which propagates at the support nose. The exception is the SMC/BMC/SMC sandwich which shows a flexural failure.

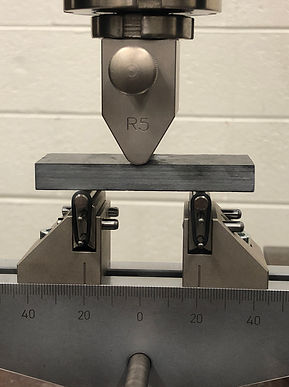
Testing Apparatus