

Glass, Heat, Pressure, and Plastics
There are two kinds of plastics that are molded. Thermoplastics and Thermosets, the former can be melted and reformed while the latter cannot. There is much debate as to which one is more ideal, but for our experiment we dealt with a thermoset. The material went through a process called compression molding to be shaped into the slabs we are currently testing.
​
Compression Molding is the process used to make the composites. As the term states, the materials are pressed using a mold while heat is applied to form into shapes. The disadvantage of this process is the wasted material. For example, the manhole covers created by Mar-Bal Inc. wasted about 40% of the material used. The goal of our experiment is to reduce that was by demonstrating upcycled material can be used without sacrificing some of the material's strength.
​

Our materials were molded at Mar-Bal Inc. in Dublin, VA. They were manufactured at 155 ton-force at 290 degrees Fahrenheit. The raw materials (SMC, BMC, woven glass fiber, and trimmed woven glass fiber), were subjected under these conditions for 170 seconds. The weight was measured for each of the composites and the combinations of sandwich structures could be found in the materials section.
The purpose of these combinations is to form sandwich structures for our composites. These structures takes a material and sandwiches it between two other materials. This creates a layers of material which when molded merges together to form a seemingly homogenous material. However, the layers can be vastly different in structure from one another and this may create some weakness.
​
Since our focus is recycling woven glass fiber, scrap material was processed before being used to compress our samples. Mar-Bal inc. Provided us with leftover sheets of woven glass fiber, which was used to test their original manhole cover. The corners were extracted and cut into 1 in. x 1 in. and 1 in. x 0.5 in. strips. For our study we called the strips Trims, and the corner pieces Mats. Both materials were used in different combinations to create the composite slabs that we study.
​
The manufacturing process was not perfect, however. The samples of pure SMC we molded at Mar-Bal, did not cure the epoxy and was already cracked at the center of the sample. It did not appear along the outer layer, but was apparent after being cut for samples. A thoery of why this may have happened may be attributed to having not enough material when molded, or not given enough time to cure.
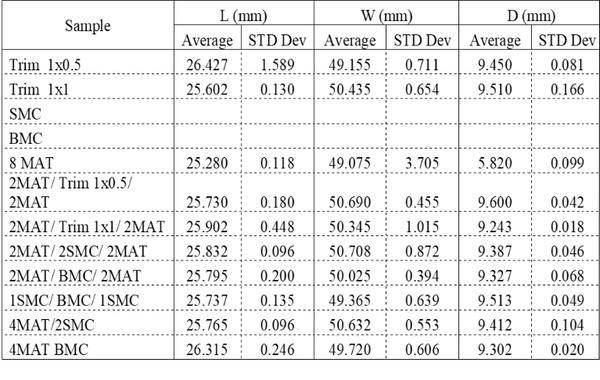
Sample Dimensions
​